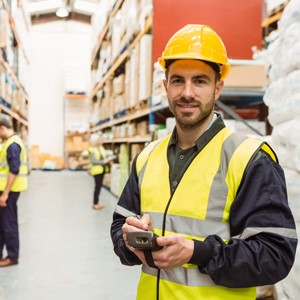
The COVID-19 pandemic has had a significant impact on the supply chain but also revealed its fundamental importance. In order to meet the new challenges that present themselves, logistics must become part of a continuous improvement programme. This is the issue addressed by lean logistics, which applies the basic principles of lean methodology to the supply chain.
Like all improvement processes inspired by the lean methodology, lean logistics targets the optimisation of supplier chains. It aims to reduce waste, the need for inventory and cycle times in order to speed up flows, reduce costs and strengthen the overall reactivity of the logistics chain. It was not, of course, COVID-19 that first brought lean logistics to the attention of supply chain managers. Yet the health crisis brought its full relevance back into focus. “It brought to light the increasingly glaring need for companies to have complete visibility of the entire logistics chain – from the manufacturer to the ‘last mile’. It showed that it was essential to be able to provide all customers, in real time, with all the information related to delivery and supply,” emphasised Grégoire Koudrine, Supply Chain Director of the Manutan Group.
A spirit of collaboration – a key element of lean logistics
To achieve this, lean logistics encourages including the supply chain in a very specific process of continuous learning, based on a genuine and transparent collaboration between all the stakeholders in the logistics chain. The aim is to encourage a dynamic of resolving minor problems daily and target continuous improvement, reliable supply and transport optimisation. In this way, if a breakdown situation arises – for example, a sudden lockdown – the supply chain can respond immediately and demonstrate very fast resilience.
“Innovation and creativity must be the key words during these difficult times. The agility of our structures and delivery methods but also the communication with our customers are essential,” explained Grégoire Koudrine. It is therefore essential to create appropriate conditions for this innovation and creation to be expressed. As a first step, the agility of distribution centres as delivery methods must become the norm in a more structured and industrialised manner.
The inescapable principles of lean logistics
Based on flow persistency, reaction speed and process agility, lean logistics offers a range of methods and tools for achieving them. These make it possible to improve the effectiveness and performance of flows in both upstream and downstream production. The methods and tools are primarily based on the following principles:
- Developing skills based on adaptability and problem resolution.
- Creating coordination structures based on a culture of cooperation and creative energy.
- Continually updating supplier risk maps but also supply risks and industrial risks.
- Maintaining a minimum stock level to cover replenishment lead times and prevent stock shortages.
- Developing “pull” systems rather than “push” ones to avoid waste and reduce storage costs.
The tools and methods of lean logistics
It is difficult to optimise flows without tracking tools. In this regard, RFID (Radio Frequency Identification) technologies and WMS (Warehouse Management System) software are clearly inseparable from lean logistics. For its part, developing a Value Stream Map makes it possible to obtain a clear and simple view of the entire logistics chain.
Finally, as it aims to make processes more effective, identifying and eliminating sources of waste is clearly at the heart of the lean methodology. When applied to stock management and logistics it primarily consists of avoiding:
- Too much stock
- Waiting times
- Transport of empty containers or movement of redundant stock
- Redundant stock
- Picking errors
- Unnecessary or insufficiently optimised movements by operators
- Deterioration of items during storage or order preparation
The 5S methodology
Originally developed in Toyota’s Japanese factories, the 5S methodology aims to create an operational work environment that continually optimises the overall functioning of the company. Perfectly adapted to supply chain organisation and warehouse management, it is inseparable from the concept of lean logistics. The 5S stem from Japanese and can be broken down as follows:
- Seiri: Remove what is unnecessary
The objective here is to eliminate anything that has no place in a warehouse so as not to have unnecessary clutter in the workspace.
- Seiso: Make things sparkle and get them clean
The idea is to always keep all the materials used in the warehouse in a perfect state of cleanliness, from the forklift truck to the pallet truck, to ensure that they constantly function smoothly and avoid the risks of them coming to an unnecessary standstill.
- Seiton: Organise the workplace in the best way possible
Organising the workspace perfectly and keeping tools and equipment tidy aims to avoid wasting time and energy.
- Seiketsu: Standardise the regulations
Standardising the principles inherited from the 5S methodology – in other words strictly observing them daily – is the way to guarantee their effectiveness.
- Shitsuke: Monitor improvements and move forward
The 5S methodology cannot be truly effective if it is not purposefully applied with discipline. It therefore requires the genuine involvement of all employees. In this way, in the event of unforeseen adverse events, all energies can be dedicated to quickly resolving the difficulty to guarantee the fast resilience of the logistics chain.
Leave a Reply
You must be logged in to post a comment.