Pallet Racking is a safe and cost-effective solution for storing palletised goods above the ground level. It is occasionally possible to block-stack pallets on top of each other, but to safely maximise your storage space, streamline your warehouse operations, and enhance overall business performance, warehouse pallet racking is the solution for you. With its numerous benefits, such as improved accessibility, versatility, cost-effectiveness, and space optimisation, pallet racking can transform your business. In this article, we will explore the benefits of pallet racking, the different types available and safety issues to take into consideration.
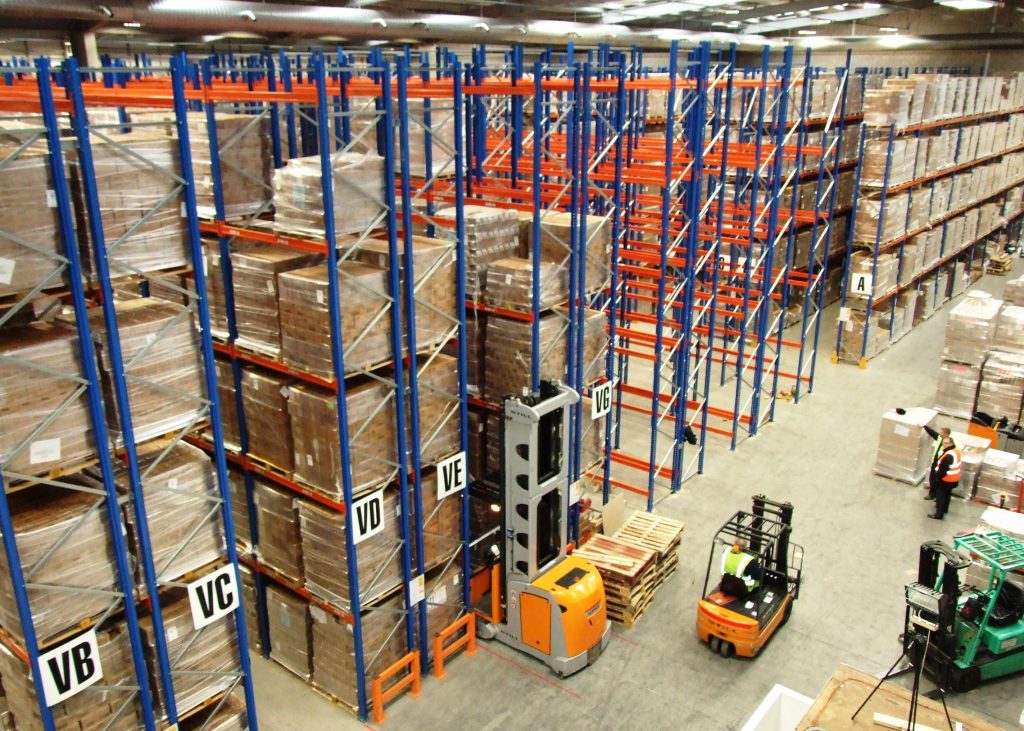
Benefits of using warehouse pallet racking
There are various benefits to using pallet racking that can transform the way a warehouse operates:
Organisation – Pallet racking provides an organised storage solution, making it easier for warehouse employees to locate and retrieve goods. This, in turn, leads to improved efficiency and reduced downtime.
Versatile – Pallet racking systems offer versatility, as they can be customised to accommodate different types of products and varying inventory levels. This flexibility allows businesses to adapt to changing demands and optimise their storage space.
Cost-effective – pallet racking systems are cost-effective, as they use vertical space efficiently, eliminating the need for costly expansions or relocations. By maximising storage capacity, businesses can avoid the expense of additional warehousing facilities.
Factors to consider when choosing pallet racking
When making this decision, several factors need to be taken into consideration.
- The size and type of products being stored will determine the design and configuration of your racking system.
- The available space and layout of the warehouse must be assessed to determine the most suitable racking system.
- The weight-bearing capacity of the racking system should be considered, as well as any specific requirements for cold storage or hazardous materials.
- It’s critical to assess the warehouse’s potential for development and scalability to make sure the racking system chosen will support any future expansion.
- The racking system must work effectively with the handling system. The ratio of aisle space to working storage space is determined by the choice of forklift.
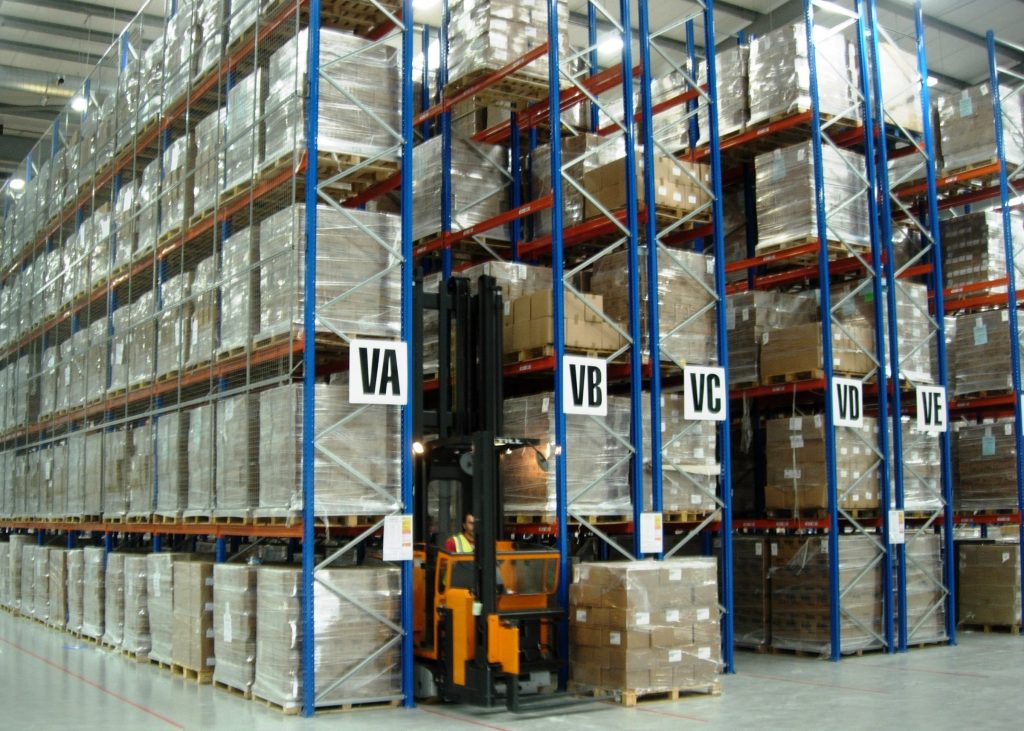
What are the different types of Pallet Racking?
Pallet Racking – Adjustable pallet racking, APR, is comprised of upright frames connected by horizontal beams to provide pallet storage levels. It is sometimes called Selective Pallet Racking as each pallet can be individually selected. It will be set out in a warehouse building in a series of single-sided and double-sided runs with each load face requiring an aisle for the forklift truck to access the racking.
Narrow Aisle Pallet Racking – High racking and long runs make the best use of VNA (very narrow aisle) trucks that don’t need to turn in the aisles. These trucks require guidance to keep on a straight path. Wire Guidance is supplied with the truck or Mechanical Guide Rail is supplied with the racking.
Heavy Duty Coil Racking – Coil cradles are fitted onto the beam levels to allow for metal raw materials storage. This requires very heavy-duty frame capacities – beyond the capabilities of many suppliers of adjustable systems.
Outdoor racking should be Hot-Dip Galvanised for outdoor use. This provides the best level of long-term protection against corrosion. But it’s not simply about an alternative finish. Outdoor racking systems must be designed to cope with snow and wind loadings on the pallets.
Drive-in racking is built in lanes where a pallet is placed at the far end and further pallets are placed above and then in front. It is a FILO system – First-In/Last-Out. A block of Drive-In Racking may accommodate a dozen or more pallets in the depth with only one load face.
Push-back racking similarly has one load face, but the truck doesn’t drive into the racking. The pallets are pushed into the system on an inclined bed of rollers. When the front pallet is removed the next one rolls into place ready for the next pick.
Pallet Live Racking – Pallets are loaded onto inclined beds of rollers and flow from a loading aisle to a picking aisle. Braked rollers control the rate of descent. Provides high-density storage with two aisles creating a FIFO (first-in, first-out) storage system.
Shuttle Racking – Pallets are placed on powered remote-controlled lifting shuttles that take pallets deep into the racking system whilst the forklift trucks are working elsewhere. A high-density storage system that will bring pallets to the front when required.
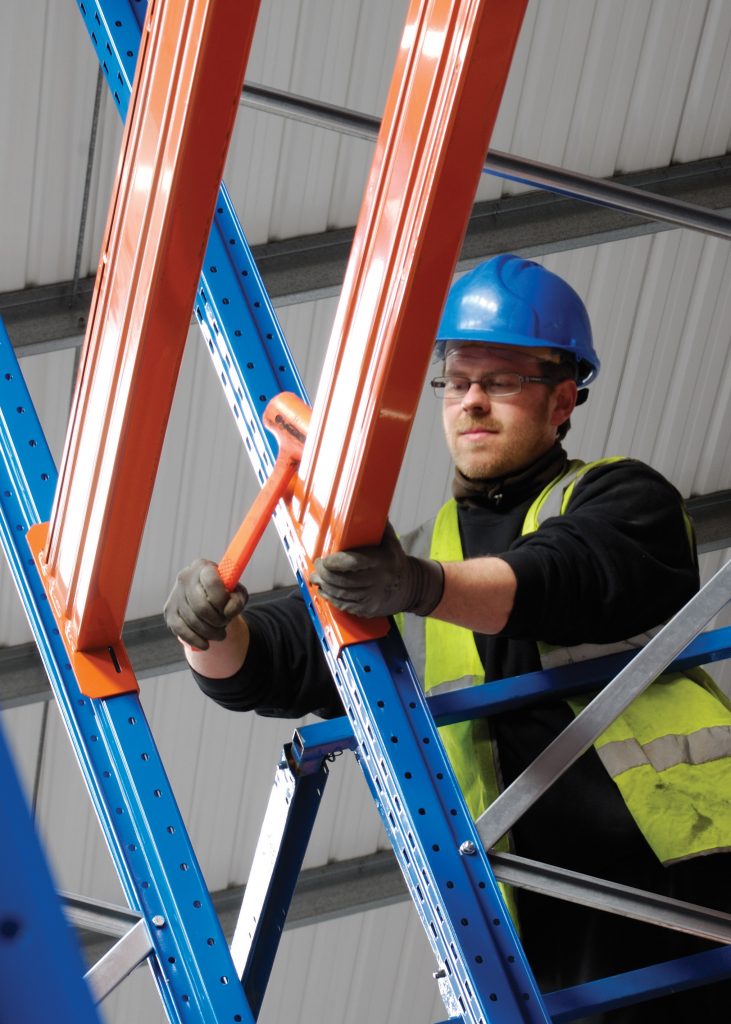
Installing and maintaining warehouse pallet racking
Proper installation and maintenance of pallet racking are essential to ensure its longevity and safety.
All Pallet racking systems require specialist installation skills. Fitters will be working at height and the safety of both the installers and surrounding staff is of paramount importance. Installation should only be carried out by experienced and suitably trained fitters who have completed the relevant SEIRS courses. Fitters will ensure that the racking is correctly assembled, secured, and anchored to the floor, ensuring stability and load-bearing capacity. They are trained in the use of appropriate lifting and access equipment such as forklifts and scissor lifts.
Regular inspections and maintenance should also be carried out by a SARI to identify any potential issues or damage. Any damaged or weakened components should be replaced promptly to prevent accidents or structural failures. Additionally, it is advisable to train warehouse personnel on the proper handling and storage of goods to minimize the risk of damage to the racking system.
(SEIRS is the Storage Equipment Installers Registration Scheme run by SEMA – the Storage Equipment Manufacturers’ Association. A SARI is a SEMA Approved Rack Inspector. SEMA work with the HSE and other bodies to ensure good practice in the storage industry. Business managers have a duty of care to provide safe equipment for their staff and should be sourcing from SEMA members or the SDG – SEMA Distributor Group).
Safety considerations for warehouse pallet racking
To ensure the well-being of employees and the integrity of the system, certain safety considerations must be taken into account.
Pallet Racking comes under the PUWER regulations (Provision and Use of Work Equipment Regulations) and must be regularly inspected. Even minor damage can lead to a weakening of the structure that could result in a catastrophic collapse of the whole warehouse storage system, so operators should be encouraged to immediately report any damage, however trivial it may seem. There should be a weekly check by a nominated PRRS, a Person Responsible for Rack Safety. This person can be trained by SEMA on a one-day Rack Safety Awareness Course. A more thorough annual inspection should be conducted by an independent SARI, a SEMA Approved Rack Inspector. In busy environments, or where frequent damage is occurring, the SARI inspection should be increased to become biannual.
Racking must have protection per the SEMA Code of Practice for the Design and Use of Racking Protection (2014). Some levels of protection are optional, but wherever a forklift turns to access a picking aisle, protection to that corner of the racking is mandatory.
Conclusion
Efficient storage is crucial to the success of any warehouse. By implementing warehouse pallet racking systems, businesses can maximise their storage space, improve productivity, and streamline their operations. The benefits of using pallet racking are numerous, including enhanced accessibility, versatility, cost-effectiveness, and space optimisation. However, it is essential to carefully consider factors such as product type, warehouse layout, and future scalability when choosing the right racking system. Safety and proper maintenance should also be prioritised to ensure the longevity of the system.
All our pallet racking conforms to the British Standard. Click here to view our range or contact us for more information.